When our customers think of where measurement accuracy and repeatability in a tag testing setup originate from, they usually mention things like output power resolution, power setting accuracy, measurement distance measured down to a millimeter, angular alignment, and high quality matched antennas, test grade RF cables, etc… My claim is, and it’s not even a bold claim, but more like a friendly reminder, that the most significant factor in achieving result repeatability and comparability is actually the environment.
So, what is the best route to a great environment? Well, clearly, the best solution is to use a closed and controlled environment like an anechoic cabinet specifically designed for RFID measurements. At Voyantic, the most iterated and refined cabinet is the C50. It is also the smallest of the offered cabinets, supporting the TIPP/ARC compatible four antenna measurement layout.
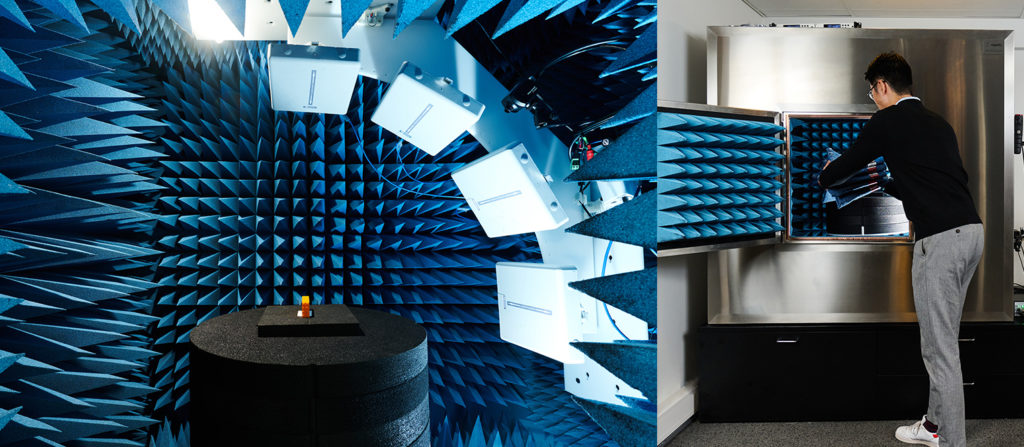
Test Distance
The C50 name comes from the 50cm nominal measurement distance and the circular arrangement of the antennas. The choice of the distance is a sweet spot to be as close as possible for best accuracy and dynamic range, but far enough to be in an accurate enough representation of a far-field for most average-sized tags, tagged items, and item stacks. Any further attempt to still reduce the distance rapidly ends up in the antennas not physically fitting anymore or just coupling into each other as they would sit in each other’s reactive near field.
The Cabinet Size
When you add on top the 50cm test distance the size reserved for the test object, clearance for the Fresnel zone, the volume required by the UHF range pyramid absorbers optimized for each wall, and the outer shielding, you still actually end up with a reasonably sized package. The C50 chamber totals to dimensions of 1,55m x 1,50m x 1,05m. This typically doesn’t sound important in any way, until one is planning the location for the cabinet and the transport route up to the very spot. These dimensions have not evolved by accident but rather designed from experience so that the cabinet would fit through as many door openings, narrow corridors, and elevators as possible. Also, the total weight remains in the 200kg range, making it movable by a few sturdy RFID test engineers without renting any additional equipment.
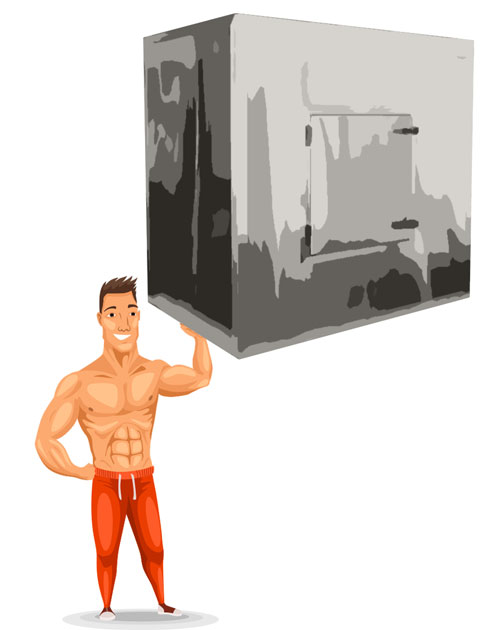
Low Reflections
One of the hardest parameters to get right is the level of unechoicity. It wouldn’t be too hard in a totally empty space, but as the item under test requires a computer-controlled rotatable platform withstanding over 10kg of weight and still being totally stealthy, things get a lot trickier. The rotation mechanism and the support platform should not provide alternative radio paths from the antenna to the tag which could create a multipath situation and decrease the accuracy.
Turntable Design
To achieve the required stealth properties, anything bulky, parallel, and flat should be avoided. Also, electrically conductive materials must be avoided at all costs, except for the shortest of screws. This means that conventional mechanical design is thrown right out of the window and other approaches are needed. Our chambers have fully ceramic bearing structures, Kevlar belts, fiberglass axles, Nylon bolts, and numerous foam structures. Most other structural parts are carefully designed from polyamide with most of the material hollowed out and any parallel and straight lines broken to reduce the RF footprint as much as possible.
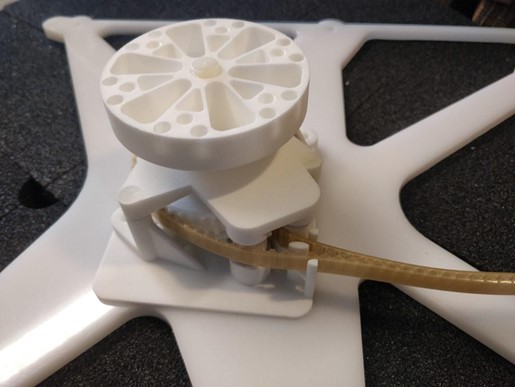
See the full range of available Voyantic anechoic chambers here ›
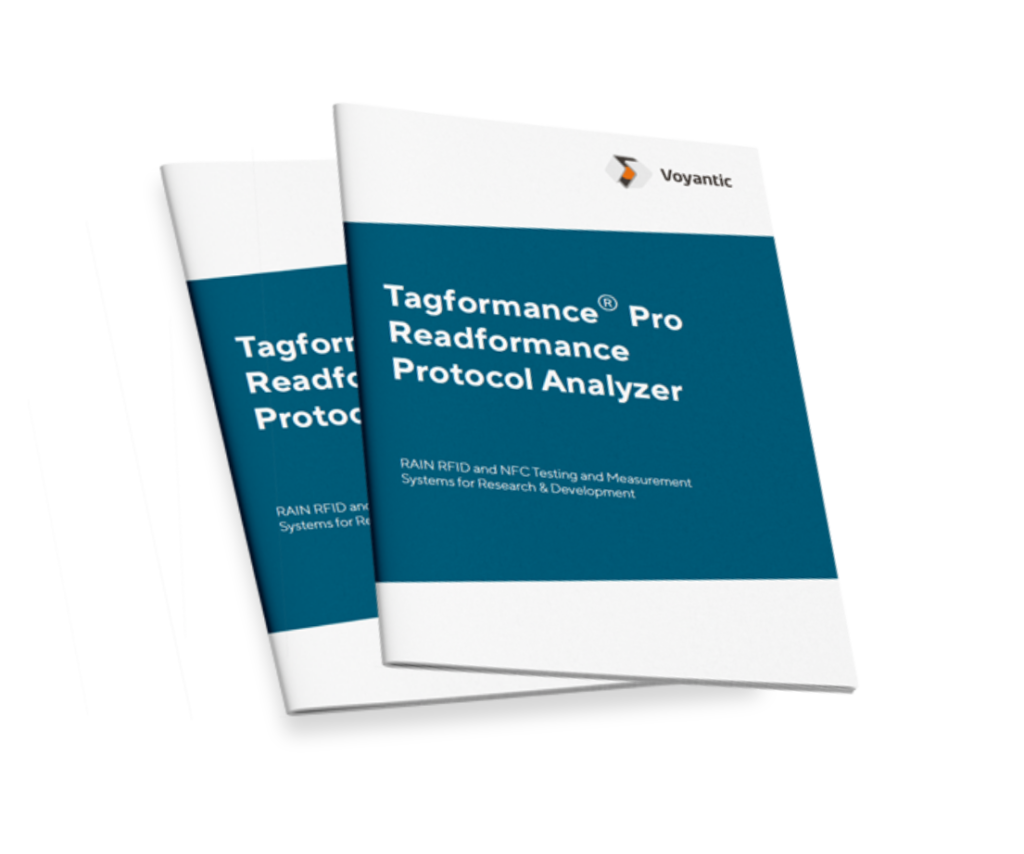
Is your RFID lab up-to-date? Download R&D Solutions Catalogue
Learn more about the Voyantic Tagformance® Pro system, accessories, and test chambers!
By combining RAIN RFID and NFC testing into one compact test device, our all-new Tagformance Pro is a true all-in-one tool for anyone either developing or using RFID technology.