Summary
- Bad RFID tag production quality = unacceptable variance in tags’ sensitivity = inconsistent performance / read ranges = unreliable RFID system performance = unhappy customers = bad for business
- Quality can only be checked with professional RFID testing and quality control systems
- Voyantic can help you improve design and manufacturing quality
Voyantic has published a lot of content about RFID technology, the market, and quality testing practicalities. But I wanted to understand what quality really means in RFID. And why should label converters and tag manufacturers care? Read on to find out what I learned.
Framework of RFID Tag Quality
The quality of RFID tags and labels boils down to RF performance – how consistent is the performance compared to the RFID tag specifications? RF quality cannot be seen with the human eye. Nor can the RF performance of a smart label or inlay be checked with any camera, x-ray, or machine vision. The quality can only be checked with RF (radio frequency) measurement system.
(Note: The other aspect of RFID tag quality, that will not be covered in this post, is tag data content. Learn more about tag data and encoding here: https://landing.voyantic.com/webinar-rain-rfid-encoding-for-barcode-professionals)
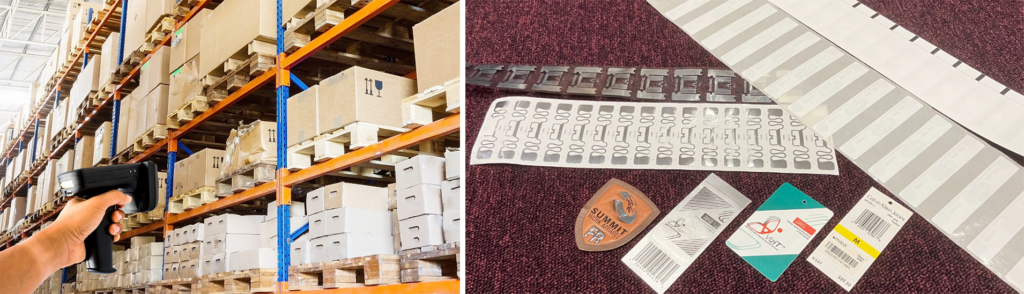
With that in mind, the following framework describes the levels of defining smart label RF quality, from design quality to documented production quality control:
- Design Quality means fit-for-purpose
RFID tags are designed for different use cases and applications. Good quality design means that the tag has the required performance and durability for the intended use case, taking form factor and unit cost into consideration as well. In practice, performance translates into readability and read range of the tag in the environment it was designed for: from how far the tag can be read, and from which angles, what type of items is it a good fit for? - Tags can be functional but not-fit-for-purpose
Taking a simple approach, the functionality of the tag can be checked with any reader – if the tag ID can be read, it is a functional tag. Sadly, this approach does not reveal aspects of quality, or if the tag meets the requirements or not.
Consider an analogy to a tag functionality test from the automotive sector: at the end of a car factory line, someone only looks at and listens to the cars: “I see a car and hear the engine – Quality check ok!” - RFID tester verifies that tags meet the specifications
A proper quality test measures the RF performance of the tag, preferably on the production line. Voyantic’s Tagsurance 3 RFID production quality control system checks the tags’ performance against pre-set criteria. The system gives a pass/fail result based on the requirements for each RFID tag passing through the system. - Knowing the production variance is the key to improving your process
Quality testing also reveals the variance in the tested tags’ performance. The variation in the tags’ sensitivity in practice means the differences in the tags’ read range. Tag sensitivity is the measure of how much power is needed to wake up a tag. Variance is inherent to mass production – manufactured tags are never perfectly identical. Quality requirements set the acceptable variance limits for the tags’ sensitivity, ensuring they meet requirements for consistent performance, i.e., consistent readability of the tags.
Knowing the variance is essential for internal development: for discovering good practices, and making comparisons – comparing machines, production teams, materials, settings, and so on. - Customers expect proof of quality
The highest level is to be able to prove the quality in detail. A professional quality control solution automatically records a log of all tests with the tag’s unique codes along the log data. This record can be used to prove the quality of the production batch and to prove the quality of each individual tag.

Why Quality Matters…
…for the RFID system end-users?
Variation in sensitivity causes the readability of the tags to vary. Differences in tags’ read ranges lead to missed readings, and ultimately, decreased reliability of the whole RFID system. High variation in tag sensitivity also indicates variation in durability – some tags may last longer than others. End users will not be happy to see the reliability of the RFID system decrease.
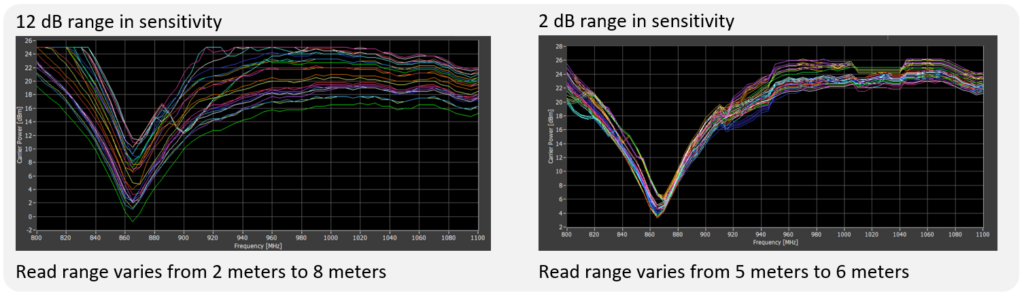
Customers expect consistency and for each tag to perform according to its datasheet information. As customers’ knowledge and experience of RFID technology increases, they also expect a documented quality program and, in some cases, require documented proof of quality from the tag supplier, and even compliance with a quality standard.
…for manufacturing?
Quality management is the bedrock of RFID inlay and label manufacturing. A complete RFID quality control system gives visibility into the production process to catch production line issues early on before more tags start to fail, thus reducing waste and improving yield.
The statistical quality data also enables comparing machines, production lines, and shifts. Good practices can be adopted, and poor performance can be addressed, improving the overall efficiency of production.
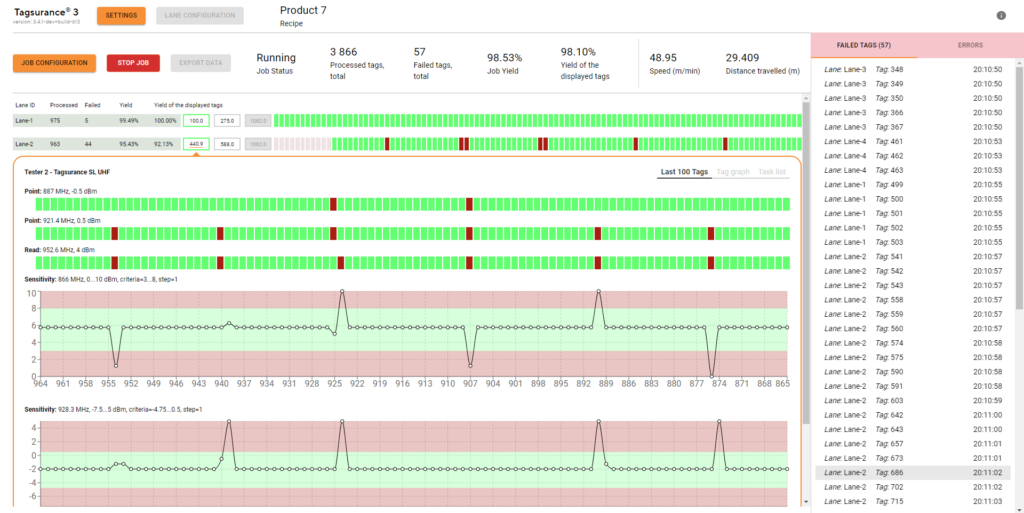
… for management?
A company’s top management typically focuses on the long-term growth and profitability of the company. High-quality products contribute to customer satisfaction, thus helping to drive more recurring sales revenue. Higher production yields, reduced waste, and increased production efficiency also contribute to better margins.
The measured quality data is the basis for continuous operational improvements and long-term profitability. In practice, data enables optimizing investments: Which machines and materials work the best, and where there is room for improvement?
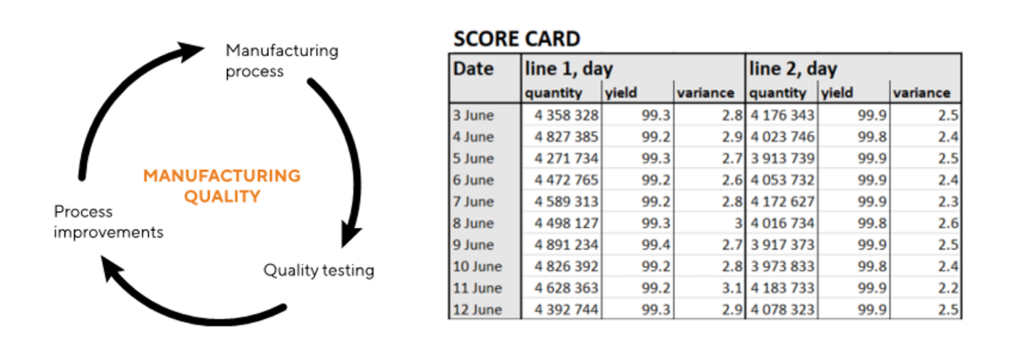
The Cost of Bad Quality
As the industrial scale of a company increases, the importance of good quality and reliability gets to a whole new level. Two very typical use cases for RFID are inventory tracking and supply chain management. Big brands and retailers may have hundreds of millions of items tracked and traced with RAIN RFID throughout their supply chain and retailer networks. If you consider, for example, that 1 percent of the RFID tags used to track items do not work well, that doesn’t initially sound too bad. But when you are tracking hundreds of millions of items, 1 percent translates into millions of products being lost from inventory tracking and considered stolen, wasted, or otherwise unaccounted for.
- Read more about the cost of bad quality: https://voyantic.com/blog/posts/analysis-of-the-cost-of-rfid-quality-and-how-not-to-lose-a-customer/
The Experts in RFID Testing and Quality Control
Voyantic’s core business is to measure the performance of RFID tags and inlays – to help our customers make sure every delivered tag works right, and enable engineers to make better products. Our vision is that every RFID tag and label have been tested and verified in the production process with our quality control system
Get in touch to see if we can help you with your RFID projects!
Learn more:
- Best practices for RFID quality testing: https://voyantic.com/blog/posts/best-practices-for-rain-rfid-label-quality-testing/