We hosted a webinar on managing quality in RAIN RFID and NFC manufacturing. During the session, industry experts shared their views on setting quality goals, on the relevant standards, and on best practices for quality testing through case examples and practical tips. While veterans in RFID quality testing recognize the need for it to achieve excellent and consistent quality, for many less experienced in the field, it can be puzzling to justify the investment for the required RFID test equipment.
With this in mind, it is worthwhile to explore whether the cost of good quality in the context of RFID is justifiable. In an earlier blog post, we discussed optimizing the cost of quality. In this post, we give an example analysis of RFID quality costs.
Analysis of the Cost of RFID Quality
Typically, the three main process steps in smart label manufacturing are chip attach, converting, and personalization. While the process details are specific to the manufacturer and machine, the analysis methods are universal:
- Failure analysis: What is the impact of possible machine failures?
- Process analysis: How do quality defects impact the process?
- Cost analysis: What is the cost of quality defects?
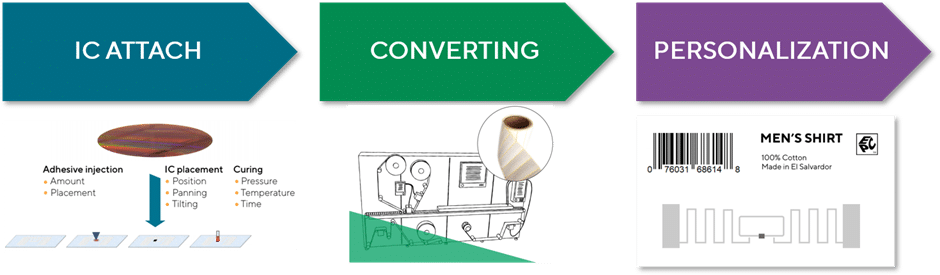
To remain in scope, our example analysis focuses on the cost impact of non-performing RFID tags in production. The case analysis is inspired by the case study presented by our customer Lab ID in our previous webinar session. In our modified case example, we are tasked with the delivery of 1 million labels to a customer. Let us assume that our manufacturing process has a yield of 98%. Out of the 1 million produced tags, 2% would be non-performing, meaning that these tags are bad quality or out of specification. Confronted with this reality, there are three possible actions to address non-performing tags which are described in the picture below.
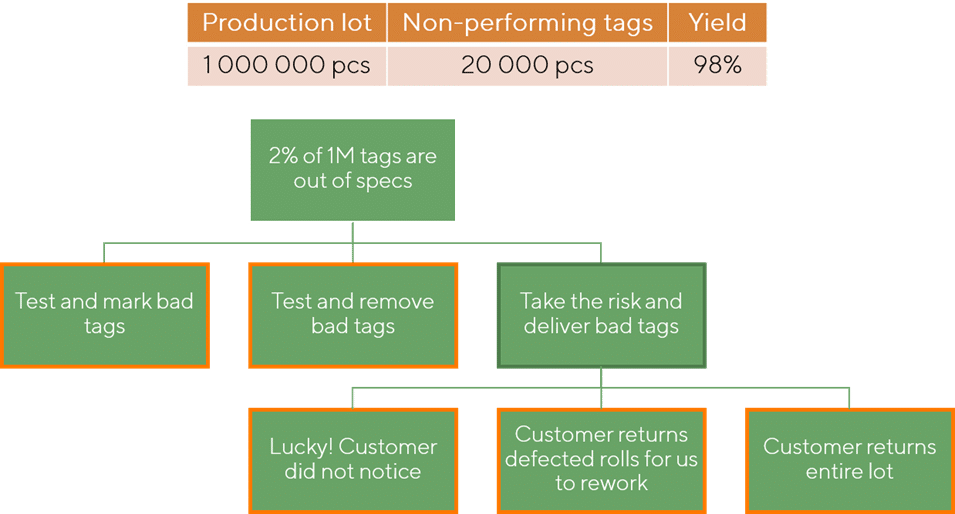
The first one is the baseline scenario for the case. We assume that cost and sell price per tag are 0.08 and 0.1, respectively. This leaves us with a margin of 20% for this production lot. In this scenario, we do not take into account any potential cost impact of 2% non-performing tags.
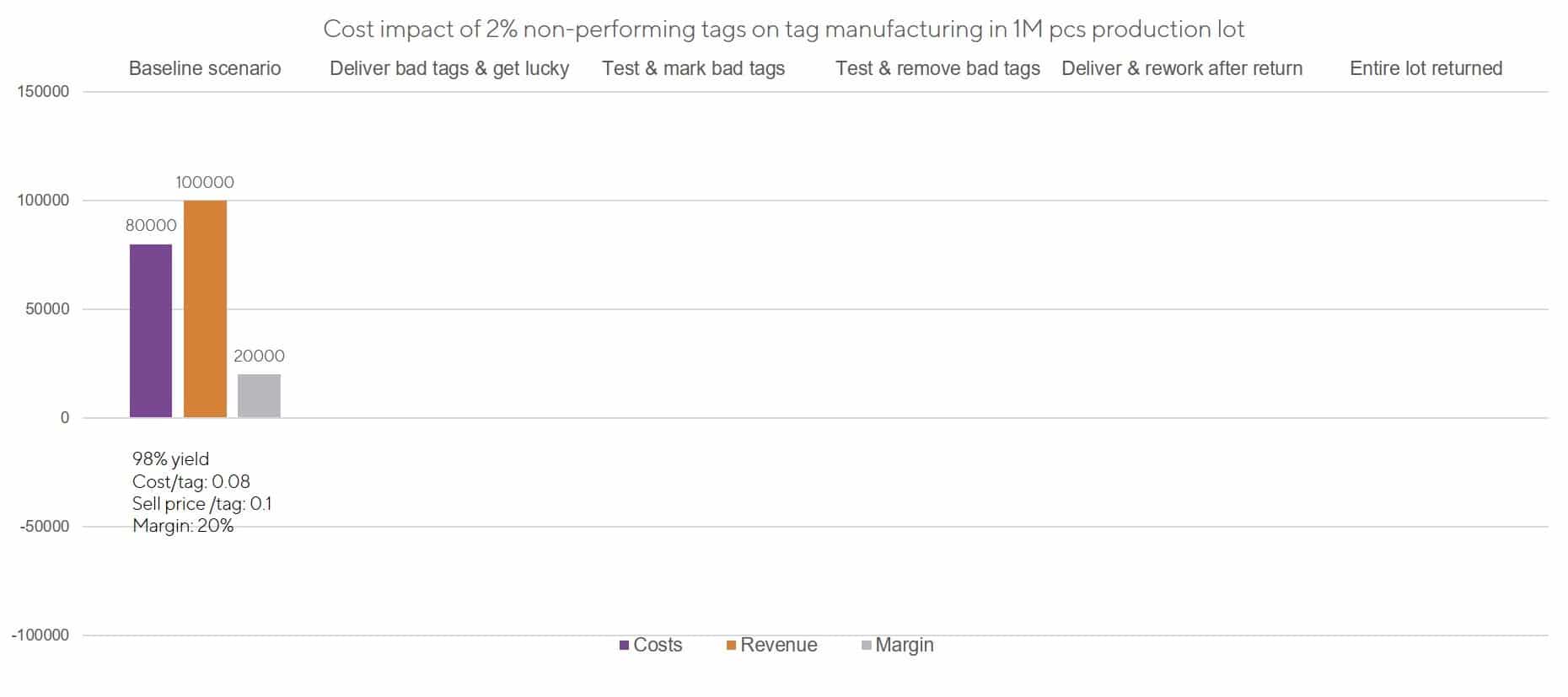
In the next scenario, we ride our luck and deliver all tags without addressing the bad ones. Thankfully, the customer does not notice any defects this time. While the 2% of non-performing tags did not have any repercussions on our margins, the last two scenarios showcase how repeating the action might bite us back the next time. We also do not consider the implications of how the bad tags will inevitably affect our customer’s business.
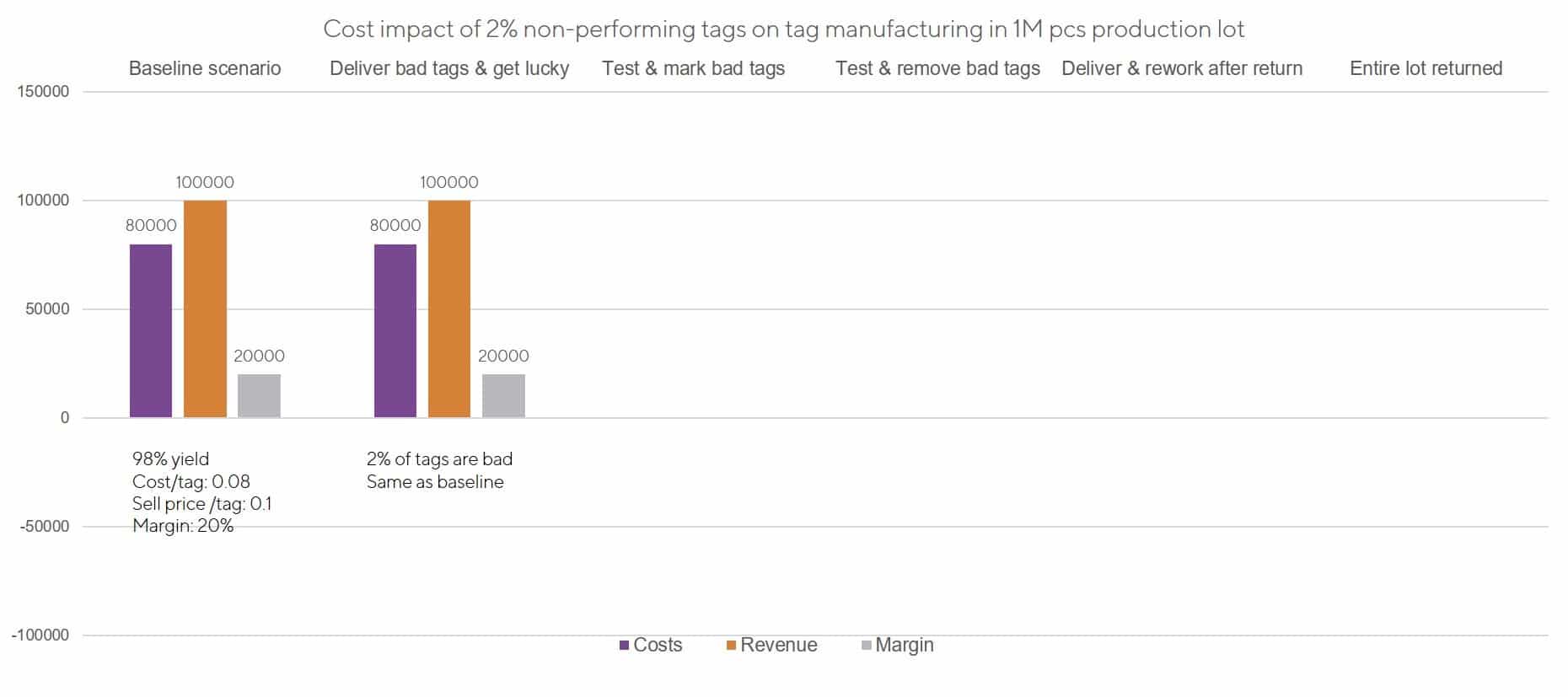
We can also do something about the bad tags. In the third scenario, we decide to test our tags and mark the bad ones during production. This would incur costs in the form of initial tester investment (a capital expenditure that is omitted from the costs of this single production lot) and marker ink (a largely negligible running cost). Marking the tags does not introduce extra production processes or require an operator to supervise the machine. With the help of the tester, we are able to mark the non-performing tags out of the 1 million. This sees our margins decrease slightly (20% to 18%) as we do not charge the customer for the bad tags.
Alternatively, we can also decide to test and then remove bad tags during production. Aside from the initial equipment investment as with the previous scenario, this also requires additional steps in the production, e.g. by handling non-performing tags with a splicing table and changing them to a normal one. This process also requires an operator overseeing the production process which induces additional costs. For our analysis, we assume this removal of a bad tag is ten times the normal cost of producing a tag. This would add a somewhat significant cost to us but our margins remain positive at 2%. Worth considering in this scenario is customers’ willingness to pay more for rolls with 100% working tags. This could help offset the extra costs associated with tag removal.
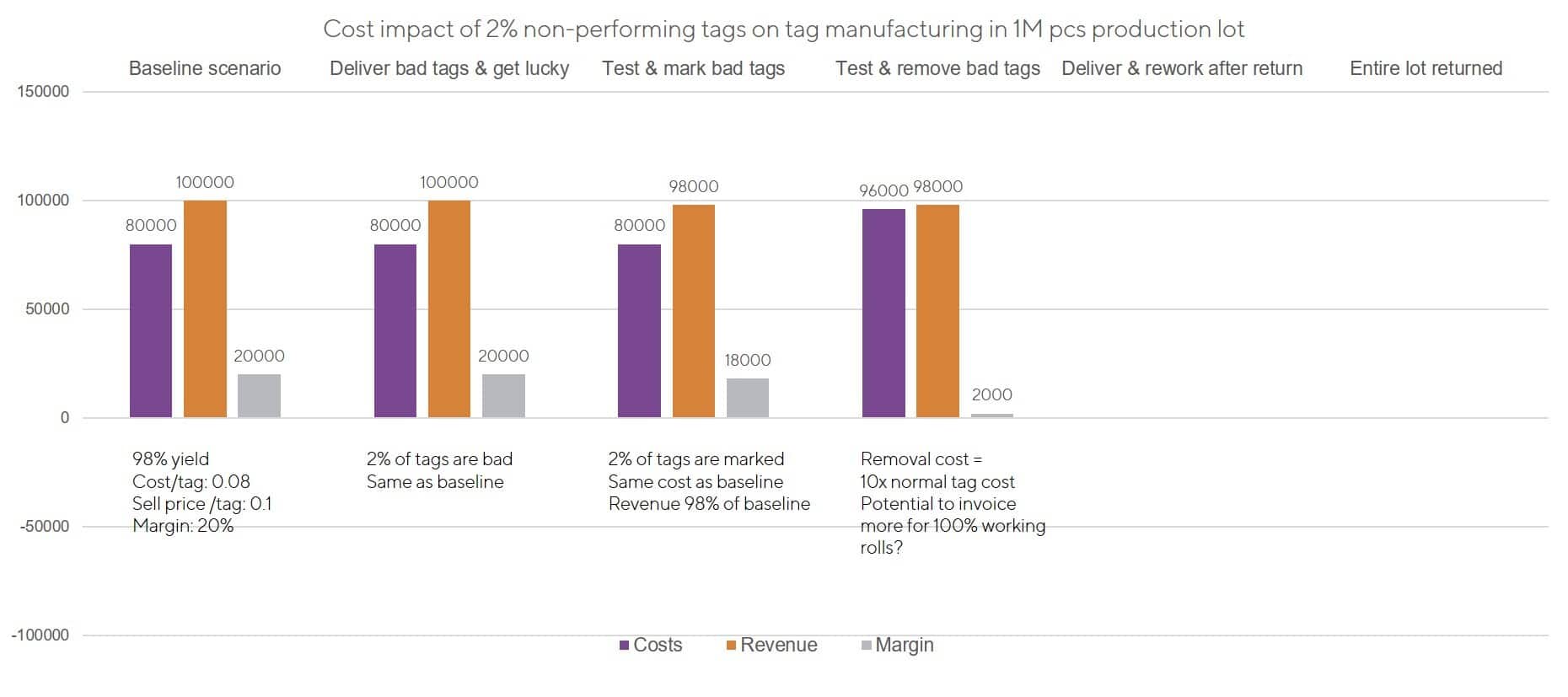
Next, we deliver all tags, 98% good and 2% bad. This time neglecting quality has consequences: the customer notices defects in our delivery, returns the lot, and demands we rework them to reach the promised quality. This requires us to find the non-performing tags from the lot and replace them with good-quality ones. For our analysis, we assume all that tag replacement hassle along with the changes to production planning costs us 25 times the normal cost of producing a tag. Not only have our margins turned negative, but we also need to deal with an annoyed customer whose plans have been disrupted.
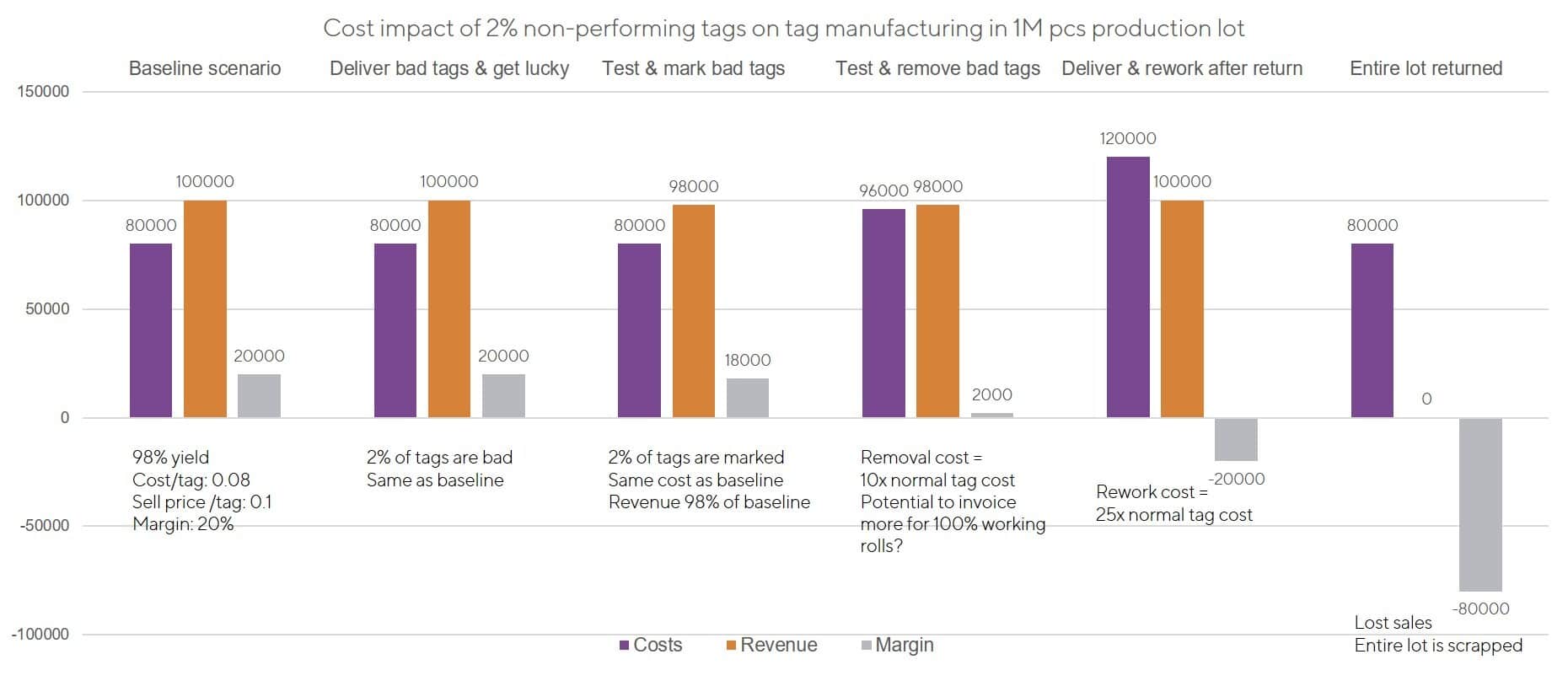
In the final “doomsday” scenario, after delivering the production lot, the customer detects the defects, simply returns the lot, and stops doing business with us. Revenue for this production lot has been lost, our customer relationship is severely damaged and our reputation as a tag manufacturer is also at risk. Not addressing quality issues and providing no quantifying proof of quality can have severe consequences. As shown, a single batch of tags mixed some with inferior quality can do much more harm than expected.
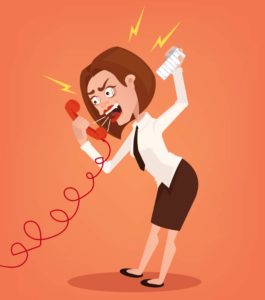
Being able to quantify quality puts tag producers in a superior position to win and establish trust with customers. Getting there requires effort but as shown in our example it is a worthwhile pursuit in the long run. We are happy to help with your needs in getting there. A good resource to start with is our webinar on managing quality in RAIN RFID and NFC manufacturing.
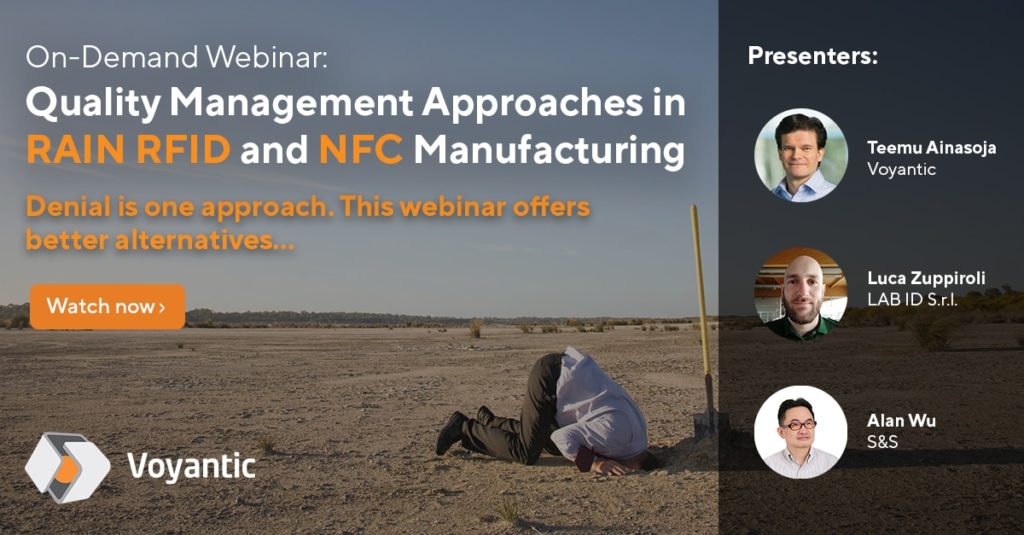