Our past two Voyantic webinars have focused on educating the label-converting industry on RFID – how to get started with RFID labels and what are the key things you should consider to succeed in the RFID business.
The first webinar covered the RFID technology basics for label converters. (If you missed it, you can watch the recording here).
For the second webinar, we invited panelists from different companies in the RFID label ecosystem, including an inlay supplier, a converting machine manufacturer, and a label converter, to give their perspectives on what is essential in RFID label converting. We also had our own expert on the panel to talk about the importance of quality inspection in RFID label production.
Check out the webinar recording or read the highlights from the webinar discussion below.
The webinar panelists were:
- Wayne Oldham, Innovation and Sustainable Technology Director at 4id Solutions.
4id Solutions is a label converter company specializing in RFID. - Axel Hess, Product Manager RFID at BW Papersystems.
BW Papersystems is a converting machine manufacturer and a pioneer in RFID technology. - Amy Lu, Global Sales Manager at Arizon RFID Technology.
Arizon is an RFID inlay and tag manufacturer, providing ODM & OEM services to RFID companies and system integrators. - Gerald Smid, Solution Specialist at Voyantic. At Voyantic, Gerald helps our customers integrate and set up Voyantic’s quality control systems on their RFID production machines.
Understanding the RFID Label Buyer Needs
When it comes to RFID labels, there is often a gap between a customer’s request and what the customer needs – the initial customer request often differs significantly from the final product they end up getting. When customers have a weak understanding of RFID technology some level of education is always required. Education is needed to make sure the label buyers understand the capabilities and limitations of the technology and to ensure they have a clear understanding of their use case requirements in order to find the right label product.
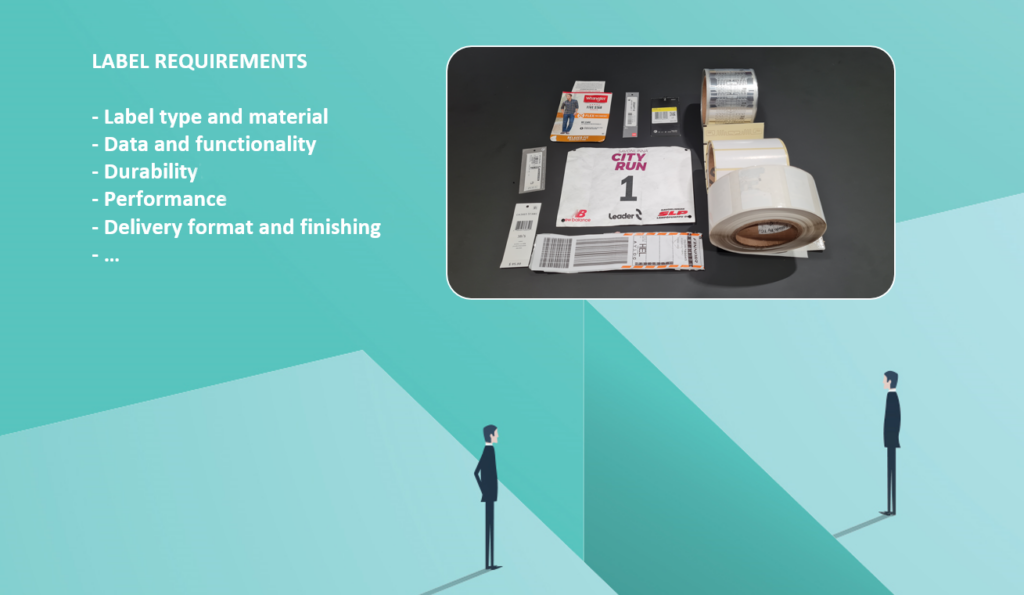
To address this challenge, companies like 4id Solutions employ a range of templates with specific questions that help in identifying the customer’s exact requirements. The questions range from technical aspects such as what frequency they need, features, performance, and data requirements to material selection, use cases, and form factor requirements. Voyantic has also put together an RFID Tag Buyer’s Guide with a checklist for label requirements and considerations.
Download the RFID Tag Buyer’s Guide here ›
For both label converters and end customers, understanding the application is also critical in the RFID inlay selection process. Some products may be challenging from an RF perspective, for example, products containing metals or liquids. These kinds of products require an inlay designed specifically for those purposes. The number of RFID labels that need to be read simultaneously also varies according to the application. In some use cases, like apparel inventory, where multiple labels must be read simultaneously, the choice of inlay becomes crucial to ensure stable and consistent performance. Inlays are always designed, and often certified, for specific applications and materials. New customers require guidance to select the right inlay for their application.
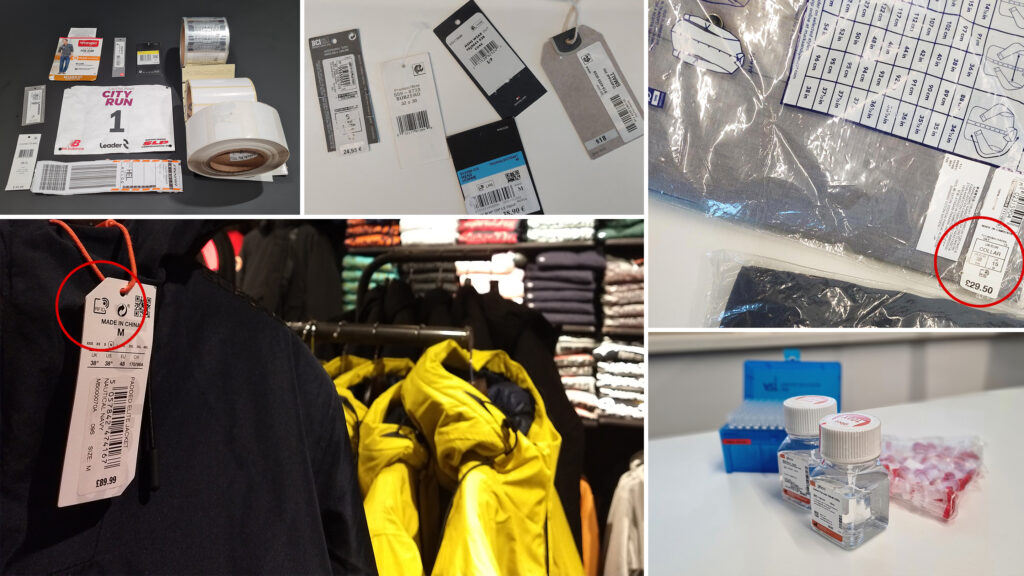
From an RFID converting machine manufacturer’s point of view, the customers’ challenges include narrowing down the focus of their RFID project. Customers must not only consider the shape and size of the RFID label but also the choice of materials, inlays (dry or wet), and chip direction. These choices significantly affect the configuration of the converting machine. The clearer the output specifications are the better the machine can be configured for a specific product.
Whether we are talking about machines, inlays, or ready labels, standardization, and shared practices within the industry could further help the industry with interoperability and drive the adoption of the technology.
Best practices:
- Ask a lot of questions from your customers to nail down requirements
- Frequency?
- Use cases and applications?
- Required read range, reader types?
- Product types, materials?
- Label physical requirements?
- Tagging specifications?
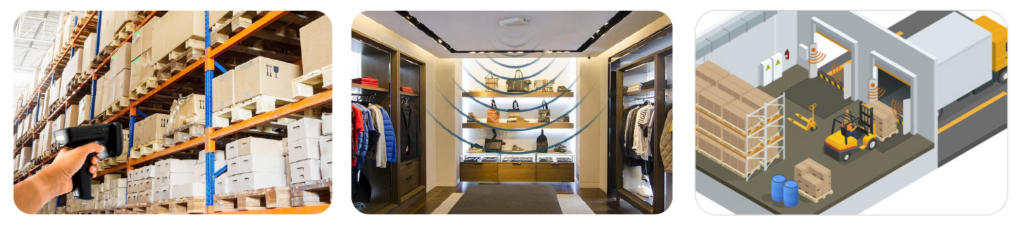
RFID Label Converting Practicalities
The biggest difference between RFID label converting and traditional label converting is that RFID labels contain electronic components that can be easily damaged in the converting process. The most effective way to avoid any issues is to understand your converting equipment, have a strong relationship with your suppliers, and ask as many questions as you can possibly think of. No question is considered too trivial in the RFID field, as asking the right questions can potentially save thousands of dollars that would be lost in a failed production run.
For a label converter, it is also important to have a good relationship with your inlay supplier to make sure you have all the latest information and understanding of the inlay materials and the impact they will have on how the materials run through your converting press. It is always better to do test runs with new materials and construction to see the impact on the converting process.
Protecting the IC within the RFID label is imperative to prevent mechanical damage. Traditional label manufacturers may focus on production speed and appearance, while RFID label converters need to prioritize IC protection. To protect against damaging the IC, there are special rollers available with IC protection (avoidance slot) or you can use special rollers with very soft materials to protect the IC from pressure.
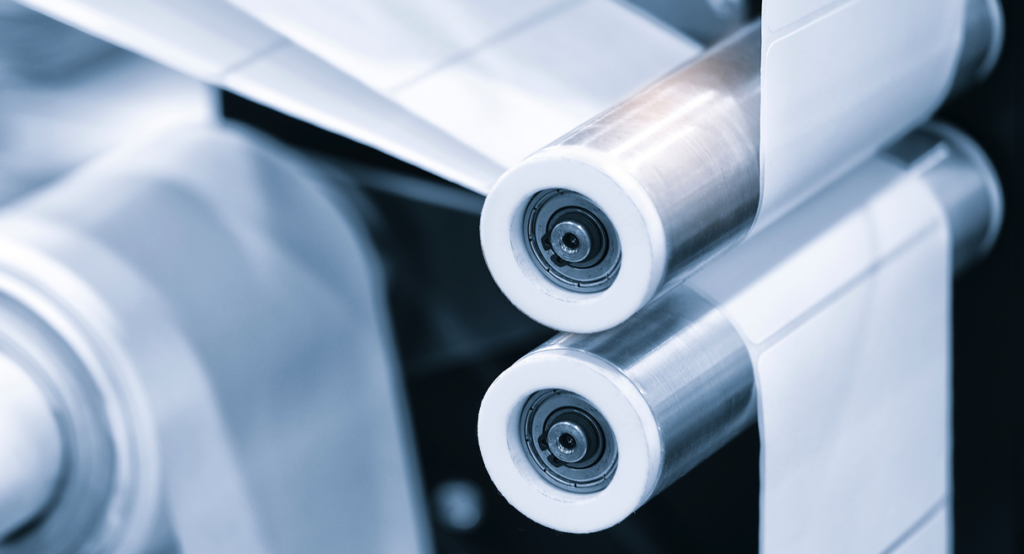
Another important aspect to consider is ESD (electrostatic discharge) protection. ESD control systems are vital, especially when exposed antennas are involved, ESD can potentially damage the tag IC.
Best practices:
- Ask a lot of questions from your machine and inlay vendors
- Know your machine!
- Do test runs
- Consider IC protection in every production step
- Consider ESD protection
The Importance of Quality Inspection
“It’s very hard to damage a piece of paper, it’s very easy to damage an [RFID] inlay when you are running it through a converting press. And it’s very easy to damage a lot of inlays very quickly when you don’t have the right processes in place.” – Wayne Oldham, 4id Solutions
For a label converter who cares about the quality of the delivered products, a proper RFID quality control system is essential. Without RFID inspection, there is no way to guarantee the quality of the labels that have been sent to the customer as RF performance cannot be visually verified. A damaged RFID label may look exactly the same as a working one. RFID label performance can only be verified with RF measurements.
A professional RFID quality testing system provides a comprehensive assessment of the tag’s performance on multiple frequencies. Using a simple reader to test that the tag responds, does not give a full picture of the performance nor assurance that the tag will also work in the end user application, from the required distance and attached to the product. A testing system is also a valuable tool for the machine operator, giving visibility into the production process to ensure everything runs smoothly.
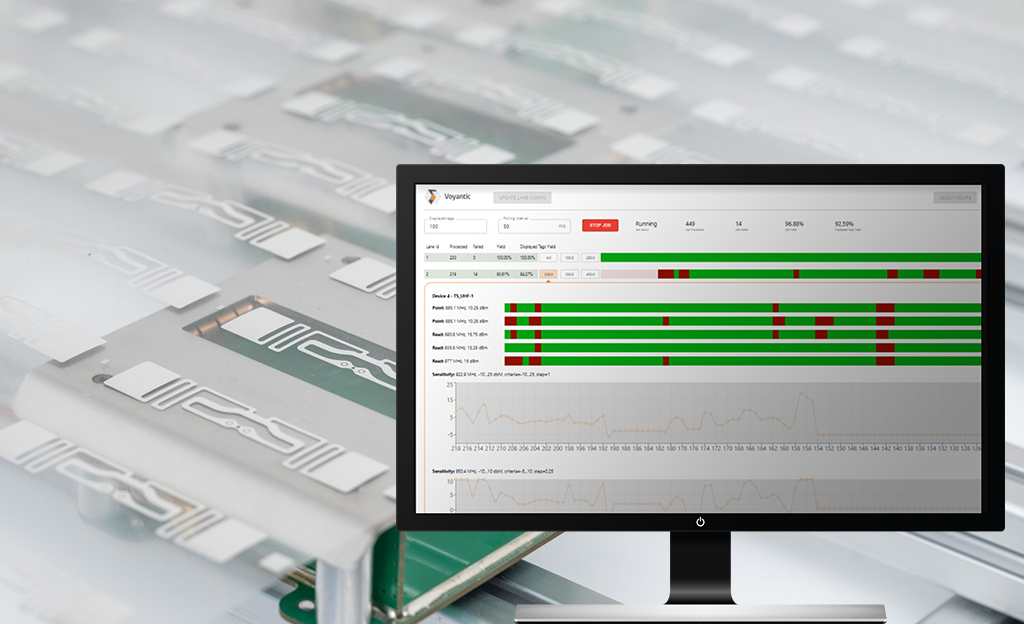
Each label must be tested individually, at high production speeds, and faulty tags can be marked, removed, or killed using chip killers or chip crunchers, depending on customer preferences. What is done to the faulty tags post-production is another important consideration for the label converter. The types of machines and processes handling bad labels also depend on the label types, for example, whether you are producing single tickets vs continuous label rolls. Some customers choose to save costs and remove the faulty, marked labels themselves in the label application process.
Best Practices:
- Test every label in the production line with a proper RF inspection system
- Choose your strategy for bad label handling
Learn more about best practices for quality testing in RFID label production ›
Long-Term Considerations for RFID Label Converters
The RFID market is growing, and long-term considerations are integral when purchasing RFID converting machines. Companies must consider their target markets, future requirements, and budget when making decisions on investments. The choice of machine impacts the types and volumes of labels that can be produced.
Although retail is still driving the market, several applications, such as consumer packaged goods (CPG), healthcare, and logistics, hold promise in the RFID industry. To stay informed about market trends, consult reports from the RAIN Alliance website. The RAIN Alliance also serves as a valuable resource for networking with industry experts and peers.
How to Get Started with RFID?
For those new to RFID converting, education, building in-house expertise, and early engagement with suppliers are crucial. Take the time to understand the technology, machines, and various aspects involved. Navigating the world of RFID label converting is a process that demands a deep understanding of customer needs, best practices, long-term considerations, and the broader RFID ecosystem. You also need to be agile — the RFID industry develops quickly, and new tag ICs with new features and functionalities are constantly introduced. However, the RFID industry also offers numerous opportunities for new converters as well as customers.
Let us know how we can help you!
All blog posts