Over the past few years, Voyantic has successfully implemented the Tagsurance 3 quality control system across multiple RFID tag production lines. These integrations not only enable the highest standards in tag manufacturing but also shed light on the positive advancements within the RFID industry. One notable development is the growing synergy between lot management and quality control. For an RFID production manager or quality manager, understanding the quantity of perfectly functioning tags in a delivery is far more meaningful than just having a count and yield percentage.
Incorporating lot management is more straightforward and cost-effective when done in conjunction with the purchase of new production machinery, rather than attempting to implement it post-machine deployment on the factory floor.
What is lot management?
Lot management revolves around the concept of a known quantity of deliverables from a specific process step. In the realm of RFID label production, a lot typically corresponds to one roll of labels.
A closely related term is “job.” A job refers to an operation dedicated to producing a specific type of product for a customer or an internal order. Importantly, the process and output remain consistent throughout a job, which may encompass one or multiple lots.
The terminology is easiest to explain with some pictures.
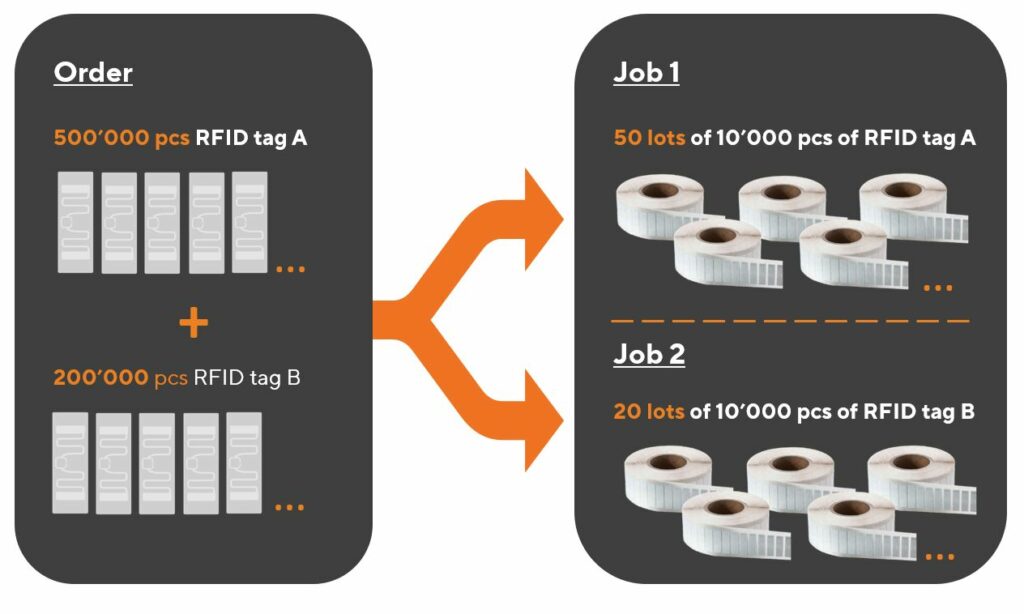
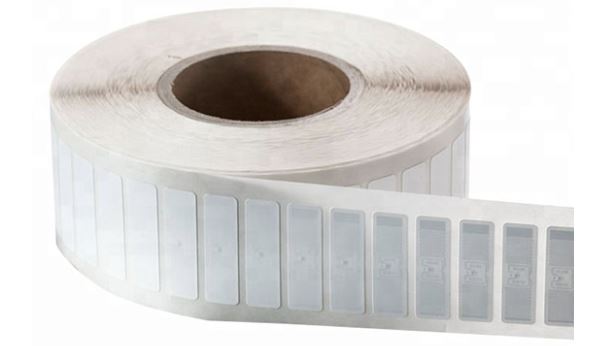
Before starting a job in the Tagsurance GUI, it is possible to define the lot. The lot definition includes details such as.
- Are all tags counted, or just the good ones?
- Is counting across lanes, or on a single lane?
- Is the lot change marked with a cut mark?
- What should the machine do when the lot is complete?
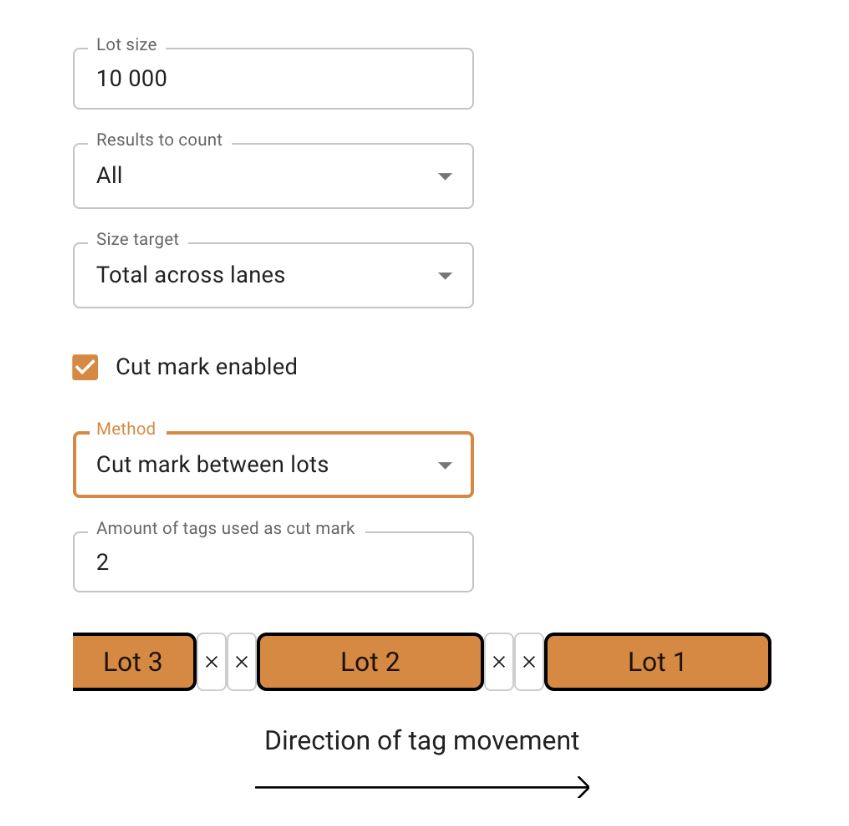
Lot management
In a typical production setup, where delivery and production are roll-based, lot management includes:
- Producing rolls with the desired quantity of labels,
- Understanding the quantity of tags within each roll, and
- Generating and reporting relevant data for each lot (each roll)
Tagsurance 3 system role in lot management
Tagsurance 3 quality control system plays a pivotal role in the seamless lot management in RFID tag manufacturing. It employs a sophisticated approach to decide whether an individual tag should be counted in the production result set, leveraging comprehensive test data to ascertain the number of tags produced on each lane, differentiating between good and failed tags.
One of the distinctive features of the Tagsurance 3 quality control system is its granular understanding of the location of each tag on the production line. It precisely tracks the lane and the distance from a trigger sensor in millimeters, providing essential position information. This combination of counts and position data serves as the cornerstone for effective lot management.
Given that the Tagsurance 3 quality control system possesses a wealth of information, it becomes the logical and secure choice to entrust with lot management. An alternative approach could involve transmitting count and fail status information to other machine components, such as the machine PLC. However, this introduces unnecessary complexity and potential risks. In high-speed production lines, even a minimal delay in data transmission (from Tagsurance 3 to machine PLC) carries the risk of misaligning counts by a single tag.
The optimal and most efficient solution is allowing the Tagsurance 3 quality control system to take charge of lot management for the following reasons:
- Precise Quantity Tracking: Tagsurance 3 is equipped to accurately determine the number of tags in a roll.
- Comprehensive Reporting: Tagsurance 3 generates and reports relevant data for each lot, providing a comprehensive overview of passed or failed tags.

When the Tagsurance 3 system manages the production lot information, the risk of split-brain problems between different systems is eliminated. Additionally, Tagsurance 3 offers the flexibility to provide precisely timed signals before, on, or after lot completion, ensuring a smooth and synchronized production process. This level of integration not only enhances operational efficiency but also mitigates the potential risks associated with data transmission delays in a fast-paced manufacturing environment.
Cut mark
The cut mark serves as a practical tool in lot management, providing a visual demarcation between the end of one lot and the commencement of the next.
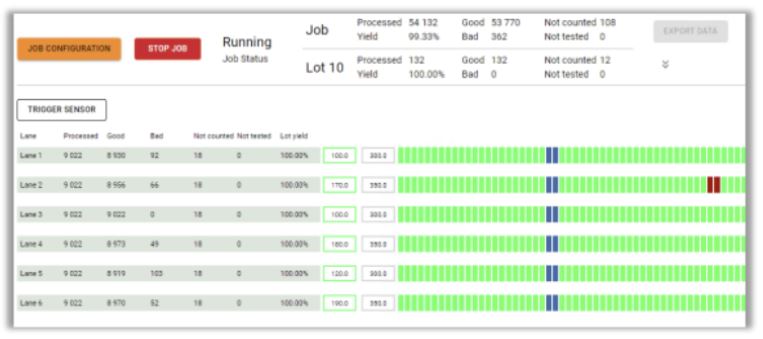
Tagsurance 3 system seamlessly integrates with the manufacturing process, triggering the device responsible for creating cut marks. In many instances, the same device used for marking failed tags is employed for printing cut marks as well.
What does the machine need to handle?
While the Tagsurance 3 system handles various aspects of lot management, the tag manufacturing machine still plays a critical role, particularly in the precise execution of cutting tasks to create the desired rolls.
There are different ways to do this:
- Automatic turret rewinders
Some machines incorporate automatic turret rewinders, presenting an efficient solution. In this setup, the production job operates continuously, and rolls are automatically cut to the correct size. This automation eliminates the need for manual roll changes by operators.
- Cut mark and manual cutting
In certain scenarios, manual or semi-manual cutting methods prove to be a better alternative. Safety considerations often drive this choice, as automatic cutters need to be well-shielded for the safety ofrom human operators.
In a manual or semi-manual process, the machine halts when the liner reaches the cut position, such as at a splicing table. The operator then manually cuts the liner before seamlessly continuing the process with a new output roll.
Selecting the appropriate cutting method depends on factors such as safety requirements and the layout of the roll handling area. Whether through automated turret rewinders or manual cutting processes, the tag manufacturing machine’s role in achieving precision and efficiency ensures the delivery of high-quality RFID tags.
Must-have machine features for seamless integration
One indispensable feature that facilitates the seamless integration of lot management with automated testing solutions is a digital IO (Input/Output) input, acting as a control mechanism for the manufacturing machine.
Stop signal input
For efficient lot management, there is a need for precise and controlled stopping mechanisms. Particularly in high-speed machines, abruptly halting operations may compromise accuracy, leading to challenges such as incorrect cutting positions on automatic turret rewinders or misalignment at the splicing table. The inclusion of a digital IO input allows for a controlled cessation of the machine, ensuring accuracy and reliability in the manufacturing process.
Slow down signal input
In practical terms, high-speed machines benefit from a gradual slowing down process before coming to a complete stop. This gradual deceleration is vital for intricate operations, such as ensuring precise cutting positions or accurate alignment at various stages of production. The machine’s ability to receive a digital IO input for initiating the slowdown process enhances the overall control and precision of the manufacturing workflow.

Serial port interface alternative for stop and slow down signals
While digital IO inputs serve as the standard for most machines, it’s worth noting exceptions, such as the utilization of a serial port interface in certain models like the Muhlbauer DDA machines. However, in general, the industry standard leans towards the effectiveness of digital IO inputs for optimal control and coordination between lot management and quality control systems.
Nice-to-have machine features for improved efficiency
Two features that significantly contribute to this efficiency are Cut Mark Capability and Operator Signal Integration.
Cut mark capability
Having a discernible cut mark on labels proves invaluable for human operators, especially when machine stopping accuracy is not within a few millimeters. This visual indicator aids operators in clearly identifying which labels belong to the previous lot and which are part of the next one. Even with automatic turret rewinders, the presence of a cut mark provides operators with peace of mind regarding the correctness of quantities.
The Tagsurance 3 system excels in this aspect, precisely triggering the cut mark at the right position. This feature not only enhances accuracy but also empowers operators with a clear demarcation between lots, ensuring seamless continuity in the production process.
Operator signal
Efficient lot management extends beyond just machine capabilities; it involves effective communication with operators. Even in the case of automatic turret rewinders or manual cutting scenarios, alerting operators when a lot is nearing completion proves invaluable. This proactive approach allows operators to prepare for tasks such as cutting the liner and changing the roll promptly, minimizing machine downtime.
The Tagsurance 3 system takes the lead by providing timely signals, either on lot completion or even a predetermined quantity before completion (e.g., 500 labels before the lot concludes). These signals can be utilized by the machine to trigger visual alerts, such as signal lights, or audible notifications through loudspeakers. This integrated communication ensures that operators are well-informed and can take prompt action, contributing to a more streamlined and efficient RFID tag manufacturing process.
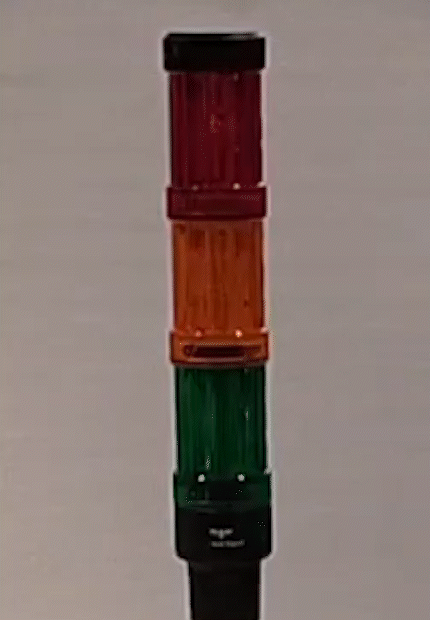
Strategic considerations for a label manufacturer to optimize lot management
The seemingly minor features within the production machinery play a pivotal role in the seamless execution of lot management. Features such as
- slow down signal input,
- stop signal input,
- serial port interface on some Muhlbauer DDA machines,
- ability to print cut marks and,
- ability to signal the operator
might appear subtle, but their absence can pose challenges in implementing effective lot management.
When investing in a new label manufacturing machine, ensure that lot management-related details are explicitly specified. The absence of connectors and signaling means can prevent lot management from working optimally. As RFID technology evolves, these features become indispensable for RFID production and quality managers seeking to elevate standards and achieve greater efficiency in the tag manufacturing process.
Connect with us to learn more about Tagsurance 3 lot management features and integration into production machines.
All blog posts