A couple of months ago, we held a webinar that addressed different environmental standards and durability requirements for RAIN RFID and NFC tags used in challenging conditions. The webinar also covered how tags typically get damaged, how damages in the inlay affect the performance of the tag, and how the durability of the tags can be tested. Our guest expert for this webinar was Richard Aufreiter from HID Global.
In case you missed the webinar and would just like to hear the main points, read on for a short recap and links to more information.
What Breaks an RFID Tag?
As a starting point for diving into the durability of RFID tags, knowing the RFID tag structure helps understand where the breaking points are and how a typical label tag can get damaged without a protective hard shell.
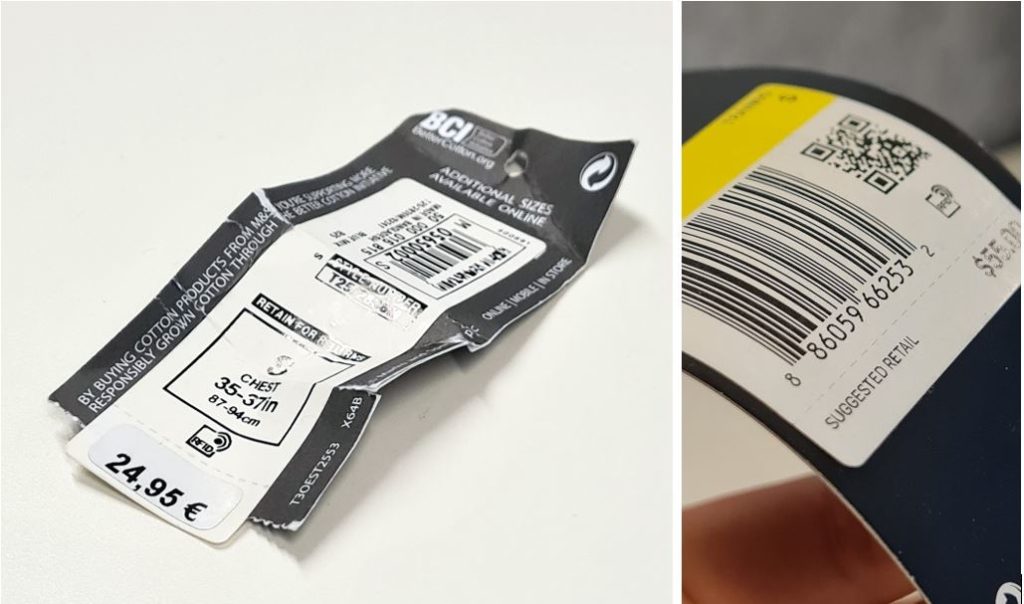
An RFID inlay consists of an IC, an antenna, and the bonding between the IC and the antenna. This inlay structure is what creates the RF performance of the tag and in practice the read range and the reading angles. The rest of the tag components are non-RFID components, e.g., the baseliner, the label surface materials, the hard case, etc.
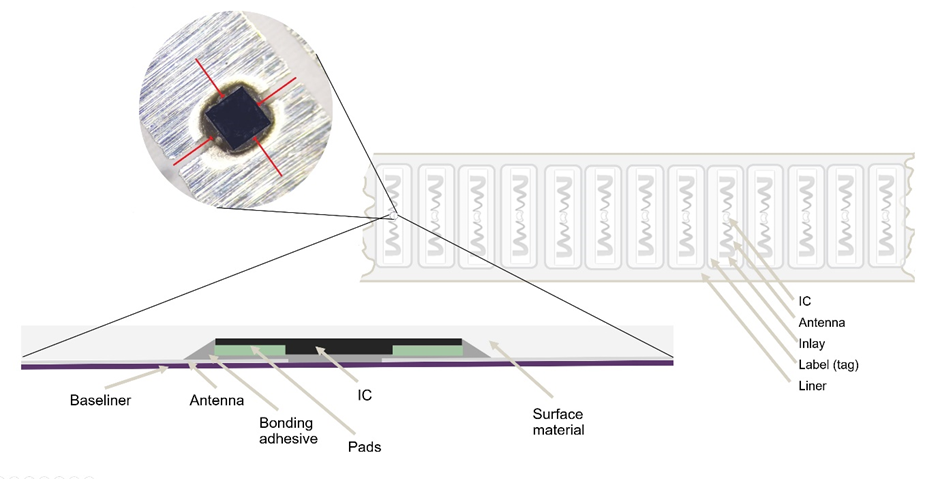
The typical part that has the most effect on the performance, and is also the most likely spot to fail, is the bonding glue between the IC and the antenna. When the tag is bent, it creates stress in the bonding glue and as a result, possible microfractures that can advance gradually in continuous use and deteriorate the tag’s performance also gradually. A damaged tag needs more power to work affecting the read range and causing tags to fail.
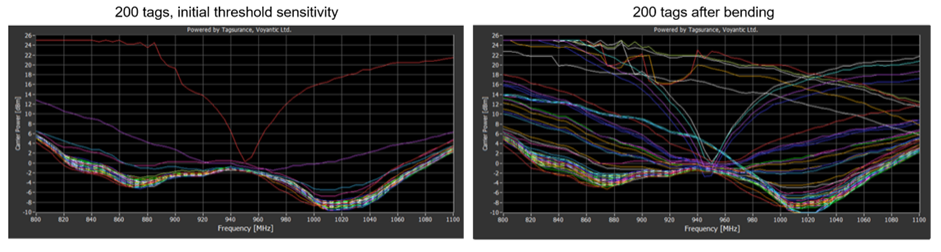
Tag inlay models have differences in durability and testing is a good way to find the most suitable design for different use cases.
Learn more about durability testing methods ›
Another reason for a tag to fail is a cracked IC. And when the IC crack, the tag typically stops working completely.
The third component of the RFID inlay, the antenna, can also get damaged. A damaged antenna typically does not completely stop the tag from working, but it affects the tuning and the sensitivity of the tag when the geometry of the antenna changes.
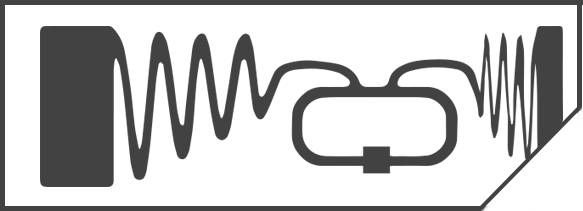
The non-RF components of the tags can also get damaged, but those damages do not typically affect the RF performance if the inlay is still intact. The damages can be cosmetic, for example, damaged print on the label. The attachment of the tag to the item can also get damaged, or the hard case of the tag may break.
RFID Tag Durability Standards in Harsh Environments
Some RFID use cases require the tags to endure harsh environments and handling. Tags may need to endure extreme temperatures, high pressure, impacts, vibration, water, etc. Examples can be found in the typical use cases of logistics, life-cycle, and inventory management, and in various industries, for example, manufacturing, hospitality, healthcare, logistics, aviation, etc.
During the webinar, Richard introduced various challenging environments, applicable standards, and testing methods for those environments. There are not necessarily standards available for all the different environments and use cases, but the suitability of the tag for the specific challenging environment should be verified with testing, nevertheless.
The typical RFID use cases for harsh industrial environments include logistics, maintenance, life cycle management, and inventory, both indoor and outdoor. Things like washing, exposure to chemicals, potential impacts, and extreme temperatures make these environments challenging.
Below, I listed the environmental standards covered in the webinar. Not every use case or environment has a dedicated certification or a standard, but the unique requirements posed by the environment should always be considered.
Yard Management in Rugged Environments
Items kept in stock need to be identified to make sure you have accurate inventory and to verify you take the right items. The tags may need to endure vibration, impact, and pressure when tagged equipment is being moved and may hit other objects in the process. Tagged items may include things like drilling pipes, shipping containers, and other heavy objects.
Vibration durability can be tested with a rattling table. Testing makes sure there are no parts inside the tag that get loose or damaged the chip or the antenna or break the housing of the tag. Pressure is also tested to make sure the housing doesn’t break. Metal housing can make the tag highly impact resistant.
See a video of HID’s tag testing ›
Related standard;
- Impact Resistance: IK rating defined in EN62262, measured in Joule
Explosive environments
Explosive environments can be found, for example, in the oil and gas industry and the mining industry. In explosive conditions, tags need to be safe to use and should not cause an explosion due to overheating.
There are two certifications that apply to explosive environments:
- ATEX (European)
- IECEx (global)
ATEX defines zones based on how explosive the environment is and what the tag needs to endure. Both certifications are more relevant for devices that are powered and not so much for passive tags.
Extreme Temperature Environments
An example of an extremely cold environment can be found in healthcare, where medical sample vials may be stored in liquid nitrogen. If you want to tag the vials with RFID, the tags must withstand that same temperature and also be readable.
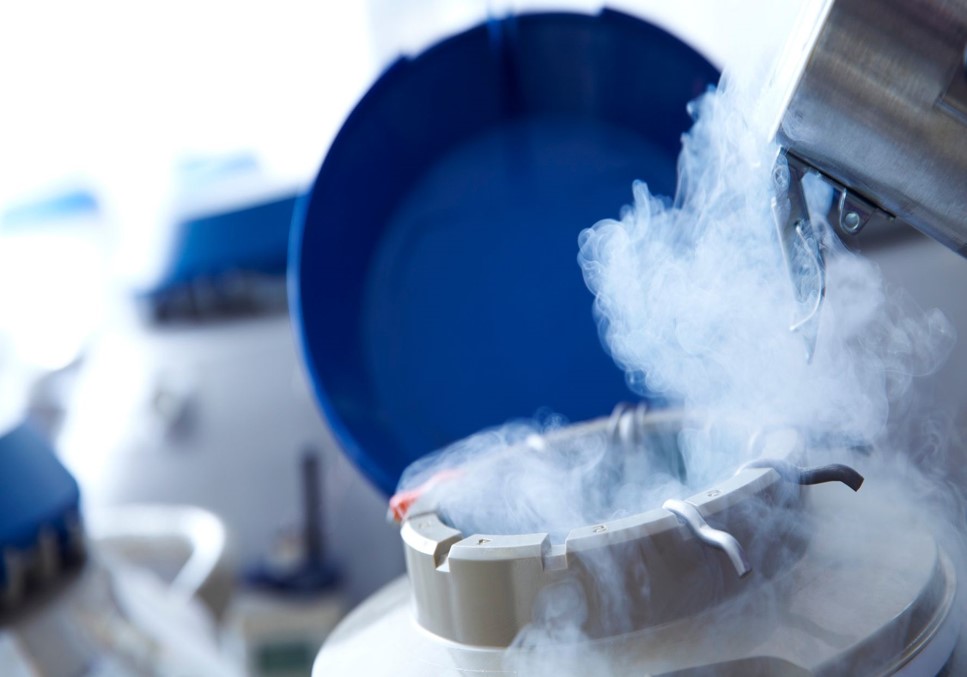
On the other end of the spectrum is flame resistance. One example use case Richard mentioned during the webinar was a tag designed to be used in an aircraft engine. A flame-resistant tag will not ignite when hit by a flame and will not burn by itself after the flame is removed.
Applicable Standard for Testing:
- UL94 HB = IEC 60695-11-10 (former ISO 1210)
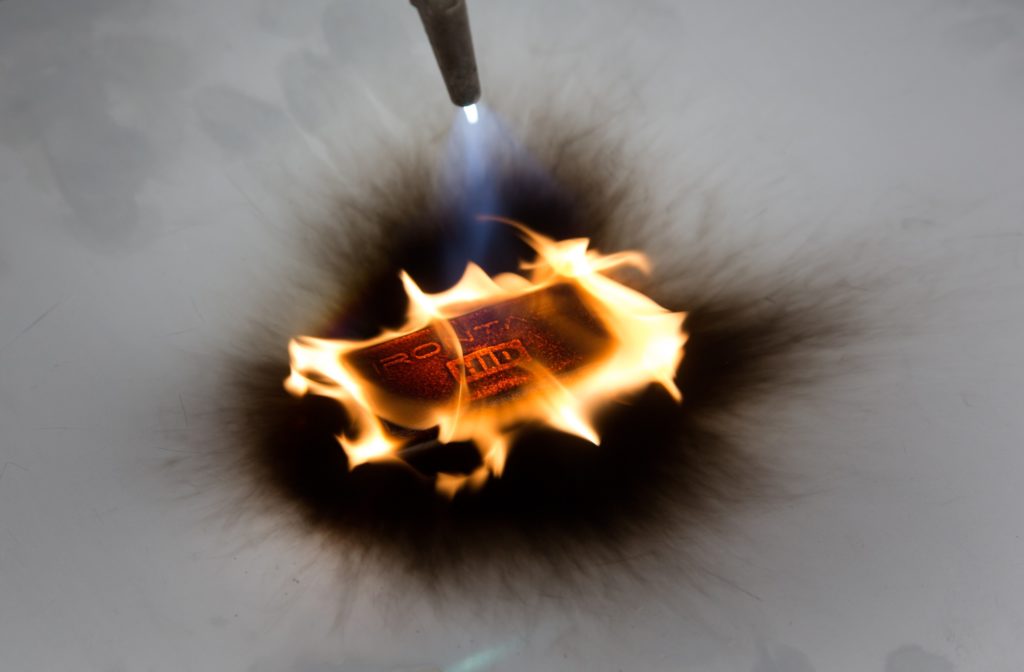
Washing Environments
Washing is a very common use case. There are different levels of washing resistance. Tags need to endure anything from a splash of water to long-term underwater submerging and high-pressure power washing. The IP rating developed by the IEC defines the level of water resistance depending on the use case need.
Relevant ratings:
- IP 66, 67, 68, and IP69K for power washing
Chemical Exposure Environment
Chemical exposure resistance also starts with waterproofness, but tags need to also endure the effects of chemicals, for example, detergents in laundry applications or sterilization in the healthcare environment. The standards for laundry are not RFID specific but they ensure that tags on textiles are safe to be used and do not pose a health risk.
Relevant Standards:
- Laundry Testing / Tags on Clothing
- ISO 15797 for the workwear washing process
- OEKO-Tex® for certifying there are no harmful substances for human health
- Medical healthcare environment
- MR – using a tag inside a magnetic resonance inspector with strong magnetic fields. The antenna cannot cause any sparks.
UV Resistance
Some plastic materials are sensitive to UV light. UV exposure from the sun and other light sources can lead to discoloration and hardening of the plastic. UV resistance can be tested in accelerated weathering tests where the item is put under extremely strong UV light that simulates a longer time frame in the real environment.
Relevant standard:
- ISO 4892-2 (Weathering)
Learn more from the webinar
One of the key takeaways from the webinar is to understand the use case and the unique factors that determine which tag is optimal for the application – defining the tag frequency (LF, HF, UHF), IC capabilities, and the tag fixing options.
Check out the webinar recording for a handy reference on the main characteristic of different RFID technologies, and example use cases with different tag types. During the webinar, we also covered tag durability testing method examples from the Aerospace and the tire industry.
All blog posts